Dyeing, Printing, Processing
`InspirOn Stenter - A Formidable Substitute To European Domain’
InspirOn Engineering, committed to serve the textile processing industry, for over two decades has made its stenter more versatile with addition of new features developed by its own R&D team of high calibre professionals.
As a part of continuous improvement on performance of stenter, InspirOn will be able to showcase at ITMA 2019, its ability to produce superior quality in very cost effective manner through following features:
1. Drying Efficiency
Achieving optimum solution for higher throughput of hot air is the prime objective in order to achieve higher drying efficiency. Series of iteration with CFD software, for nozzle development, finally resulted in the development of unique “Uniflow” air flow system by R&D team. Drying efficiency of the new model of InspirOn stenter is observed and certified by both DKTE and customer as, 15%higher than the earlier model.
2. Extra efficient machine achieving substantial saving in energy cost (Thermal+Electrical)
This has prompted corporate customers in India and also US based technical textile processors to opt for Inspiron Stenter Technology. The decisions have been reflected in achieving promised speeds and excellent quality that InspirOn stenter frame easily delivers, while at the same time consuming less thermal and electrical energy. InspirOn Engineering has emerged with its new stenter model, as a complete technology solution provider for textile finishing industry.
InspirOn stenters have proved their performance at facilities of its corporate customers like Arvind, Raymond, Vardhman, etc., to name a few, where considerable savings in thermal and electrical energy have been achieved. Repeat orders from corporate customers is obvious as customers are delighted with InspirOn stenter performance. Arvind today has 13 InspirOn stenters installed in its facilities, Raymond has nine InspirOn stenters. Many customers have shown immense faith in InspirOn by investing in its stenter installations by repeating their purchase orders.
At several corporate customers, the InspirOn stenter and European stenter are working next to each other in the same processing unit. InspirOn conducted trials under controlled conditions with automation on its own as well as European competitors’ stenter applying similar parameters both in terms of fabric as well as operating conditions. In all such trials, it was found that thermal energy consumption is lower by 10-15% and electrical energy consumption is lower by 15-20%. This is evident from the trial results as mentioned below.
The above savings shall certainly translate into substantial cost reduction per unit of fabric processed.
Squeezing efficiency
High squeezing Padder was developed by our R&D team with following parameters:
- Robust compact frame structure
- Optimised trough capacity to reduce drain losses substantially (up to 60 litre)
- Pneumatically controlled sliding and tilting trough with user-friendly operation of lifting, level controlling and cleaning
- Padder load capacity is increased up to 12 ton, maintaining uniform force of 50 kg/cm throughout fabric width through high squeeze Triflex® Rollers
- Padder design ensures, extreme low fabric tension ensuring minimum fabric elongation and horizontal fabric guiding through the padder rollers
- Higher squeezing capability ensures optimum pick up % with delicate treatment for specific processes e.g. wet on wet finish with desired add on % next, resulting in better productivity.
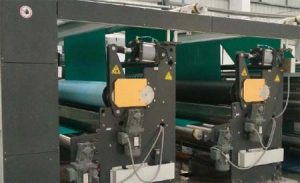
After conducting extensive trials at the R&D Centre on various substrates, the newly developed 12 ton High Squeeze Padder with Triflex roller, was installed at Somany Evergreen Knits Limited, Solapur in November 2018, for field validation and comparative evaluation of the squeezing efficiency.
Performance trials of the padder was conducted by InspirOn development team with single jersey quality of GSM 150 and width 183 cm of knitted fabric to evaluate the squeezing efficiency. Pick up in the particular quality is observed in between 70-75%, which is quite in line with the observations shared by the delighted customer for various qualities in reference to productivity of the MOTEX 15000 stenter. Results of squeezing efficiency are comparable to the one being observed on padders supplied along with world’s best manufacturer of stenter.
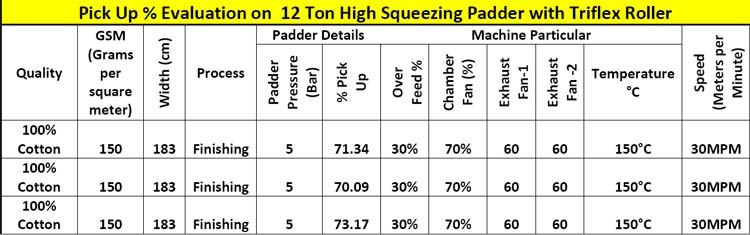
Rubber Coating agency has also audited the rollers (after running for six months) for rubber compression characteristics, dimensions, hardness stability, surface finish, all were found in good condition.
InspirOn is advancing in the field of automation in keeping with Industry 4.0 with Process Automation, SCADA system and latest web app for remote visualisation of HMI screen via smart phone or tab devices.
4. Process automation

Own controller (with imported sensors) process automation and control system, (residual moisture, exhaust humidity and dwell time) enables InspirOn stenter to process the fabric in controlled condition. InspirOn process controller with imported sensors ensures quality, consistency in product with energy efficient working.
5. Automation design to control quality of the end product and monitoring the same through self-developed SCADA system
Industry 4.0 requires two way communication between machine and systems in order to meet the exact demand from the user industry. It is important to ensure and monitor the parameters set on the machine and actual performance. Various machine inputs are converted into detailed output giving a real time context. SCADA enables the processor to monitor, analyse and evaluate the process conditions for desired quality characteristics and productivity. With SCADA it is easy to compare, evaluate the processes, parameters, accurate diagnosis of the issues, study and comparative analysis between the machines in terms of process parameters (temperature profile, exhaust humidity/ initial and residual moisture values, dwell time with speed) efficiency, productivity, thermal and electrical cost i.e. ultimately the process or passage cost/ kg.
6. Remote access not only for trouble shooting on the stenter by InspirOn but also for stenter user for process control through remote visualisation on tablet or smart phone.
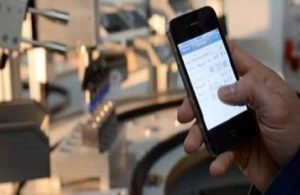
Remote visualisation on smart phones assist the processor with online view of the machine operation. It enables connectivity of third party tablet with Stenter PLC and HMI network over internet with smart tools. Remote visualisation provides log information, alarms, alerts and machine monitoring. Due to exact replication of HMI screens on tablet it is easy to operate.
Considering the cyber security over internet, user authentication with closed loop is provided.
The latest version of InspirOn stenter is capable of producing desired finishing effects for shirting and suiting which normally processors feel by hand. Thanks to the mechanical, electrical and electronic features which in combination enables machine to reproduce same process parameters ensuring the desired finish of fabric on repeat runs.
InspirOn stenters are marketed under the brand name of Motex 15000 in India and under the brand name of “SprintOn” in overseas markets. Technology for Motex 15000 as well as SprintOn is developed exclusively by InspirOn.
Textile Excellence
Previous News
liva promotes sustainability through livaeco plantable garment tag
Next News
mimaki engineering to showcase cutting-edge digital printing tech at itma 2019