Dyeing, Printing, Processing
CHTC FONG’S At ITMA 2019
CHTC Fong’s International Company Limited, together with its subsidiaries, will present its latest technologies at Hall 2, Stand D101. The latest innovative and flagship products will be on display from FONG’S, THEN, GOLLER, MONFORTS, MONFORTS FONG’S and XORELLA (Hall 6, Stand D203).
THEN SMARTFLOW High Temperature Dyeing Machines, Fong’s TECWIN High Temperature Dyeing Machine and ALC Automatic Liquid Chemical Weighting and Dispensing System, GOLLER KNIT MERC Mercerizing Compartment, MONFORTS FONG’S MATEX ECO APPLICATOR, MONFORTS Montex Stenter and TexCoat, and XORELLA Control Unit will be showcased in upcoming ITMA Barcelona 2019.
THEN SMARTFLOW : Hydraulic High Temperature Piece Dyeing Machine
THEN SMARTFLOW TSF is designed to achieve the lowest possible energy and water consumption rates available on the market for jet dyeing, with achievable liquor ratios for a full load up to 300kg with a reduced kier volume and a liquor ratio down to 1:3.5 for cotton and 1:2.5 for synthetics.
FONG’S EUROPE has a number of patents pending on the innovative new features of this machine, including the SMARTFLOW’s fabric transport design. This is based on a smart, winchless fabric transport system which eliminates the need for a loading rope, and a circular plaiter with programmable rotation speeds which provides full filling of the drop zone.
The chambers can accommodate variable loads in terms of both weight and material type down to 40kg for extremely flexible processing, and each SMARTFLOW TSF unit can be equipped with up to 8 chambers, in order to fully maximise productivity, while taking up to 40% less floor space than competing systems.
The newly-developed nozzles and reel-less transport in combination with smart controlled circular plaiting and variable chamber adjustment provide even fabric treatment without entanglements and the highest loading capacity with the lowest kier volume.
Another innovation is the new bath preparation unit (BPU) and its patented satellite tank. As the process times of jet machines have been continuously optimised over the past few decades, they have required an increasing number of service tanks for dyes, auxiliaries and hot water, adding both expense and additional space requirements. New BPU and satellite tank, with its automatic dosing and mixing programmes, working in combination with the THEN temperature management system, ensures the recipes are supplied in exact quantities, with dyes and auxiliaries well diluted and heated to the required temperature extremely rapidly.
THEN SMARTFLOW allows fully reproducible processing with the optimised use of raw materials, water and energy, for perfect dyeing every time. Hydraulically driving the fabric without the use of a transport winch opens the door to reducing the tension during treatment and results in the highest relaxation of stretch and spandex fabrics.
FONG’S ALC : Automatic Liquid Chemical Weighting and Dispensing System
Fong’s ALC Automatic Liquid Chemical Weighting and Dispensing System realizes unmanned dispensing according to the instructions fed from the Enterprise Resource Planning (ERP) system using advanced computer control technology. By means of precision mass flow-meter and metering pump, the liquid chemicals are accurately and precisely delivered and weighed from storage tanks, and with the application of valves and pipe network connections, the chemicals are accurately and rapidly distributed to the designated dyeing machine in the most effective way. With the efficient cleaning function after each delivery, not only is the operation efficiency of the dyeing plant improved but also it avoids human errors. Thus, dyeing quality is guaranteed.
FONG’S TECWIN SERIES : High Temperature Piece Dyeing Machine
TECWIN High Temperature Dyeing Machine, with its premium quality and focus on “Lower Cost, Higher Quality and More Eco-friendly”, injects infinite vitality to the textile industry. FONG’S TECWIN is designed to satisfy the ever-changing market demands. The reliability and versatility of the machine are improved.
TECWIN is equipped with several patented designs:
- Combined Air and Front Spray Nozzle – It increases the degree of dye liquor interchange before passing through the main nozzle. Moreover, Optional blower is equipped. High pressure aerodynamic flow in spray nozzle is provided to resolve the special fabrics that demand high quality.
- Automatic Adjustable Nozzle - Adjustment of nozzle setting is automatically done by means of motor drive system, and hence manual changing of nozzle is not required.
- Liquor Dispersion Storage Chamber- This is a uniquely design chamber for providing a better liquor dispersion effect.
- Upper and Lower Overflow
-Lower Overflow: Maintaining pump operation with low water level to prevent disturbance caused by rinsing at a high water level.
-Upper Overflow: This is adopted for conventional overflow rinsing function.
Furthermore, the dye liquor separation is specially designed in TECWIN. With the use of the variable loading storage chamber, the dyeing operation can be performed more smoothly and fabric patterns can be more organized, which eventually leads to a lower liquor ratio.
GOLLER KNIT MERC : Mercerizing Compartment
GOLLER will show a compartment of its KNIT MERC mercerizing machine. Goller new knit mercerizing was developed to achieve highest quality mercerizing of knit fabrics with lowest tension and upmost best dimension stability (< 3%) over the fabric width for perfect dyeing results.
This new mercerizing compartment is the result of our consequent R&D developments and follow up of our latest “SINTENSA CYCLONE” drum washing compartment`s for highest washing efficiency with lowest tension.
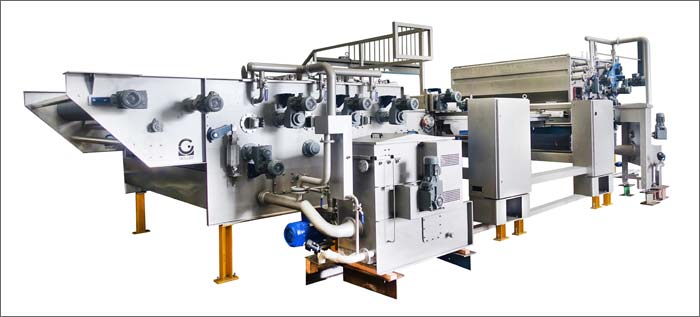
Fabric content 8,4 mtr. in impregnation compartment plus 4 mtr. in first chain section which gives a production speed of 25m/min by 30 sec dipping time.
- Dry on wet mercerizing
- Cold or hot mercerizing
- Inlet with scroll roller and slat roller for fabric guidance
- Tandematic uncurler in front of rubberized de- airing roller
- Grooved bottom roller with 320mm
- 600 mm perforated upper drums
- Automatic tension regulation
- Low liquor content integrated lye tank with circulation and Auto filter
- 8ton high efficiency squeezer on exit before chain section
- Cast iron pin chain with edge sensors, Tandematic un-curler and overfeed device
- Driven belt arrangement for fabric support
- Overflow wires incl. circulation and filtering for stabilizing
- 5ton squeezer at exit of chain field
GOLLER KNIT MERC : MONFORTS FONG’S MATEX ECO APPLICATOR
With technology support by A. MONFORTS in Germany and high production capacity in China, there are more than 3,000 sets of MONFONGS stenter frame as well as other ranges in service for customers since its establishment in China in the Year 1999. From launching the cutting-edge stenter frame range MONTEX 6500 in 2010, this new model machine has attracted wide attention in the industry and is in service to main textile base worldwide, such as India, Bangladesh, Turkey, Central and South America and South-east Asia, which led to a substantial market share and first-class reputation for Monforts Fong’s expansion in the overseas market.
The cutting-edge fabric processing applicator – MATEX ECO-APPLICATOR
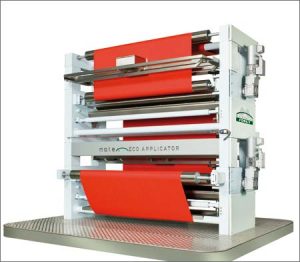
The conventional process of drying the fabric with wet pick up in Stenter process will cause large heat energy consumption, particularly it needs to heat up and evaporate water from the fabric. Our Eco-Applicator will be different from the tradition way but to be the solution to save the energy from this part of processing.
Minimum liquor application device with driven liquor rollers. The alternative to padding. For energy-conscious and cost-cutting drying. Reduced liquor content for lower remaining liquor in the trough. Universal application: Liquor application to one or two sides or different liquor application on front and reverse side.
MONFORTS MONTEX
Dyeing-, Finishing- and Compressive Shrinking Machine Manufacturer A. Monforts Textilmaschinen GmbH & Co. KG, in line with its continuing theme to providing solutions for both economy and ecology will be showing a wide range of advanced innovations and developments at ITMA’19 in Barcelona, Spain including exhaust air cleaning and heat recovery with automatic cleaning for its thermo treatment machines.
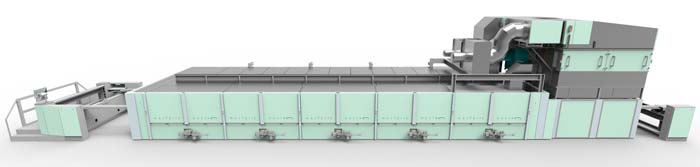
Furthermore it continues to offer the best technology in the marketplace including new improved features:
- New patented sealing devices at inlet and outlet Monforts “bionic fin®” for less heat loss and improved energy efficiency.
- New integrated, modular “Eco Pack” unit for individual configuration with heat recovery module, exhaust air cleaning module, UV-zone module for odor remove. For achieving no visible smoke coming out of the stack.
- New energy improved stenter design measures with improved sealing of the chamber and preheating of the combustion air option. All measures together lead to overall reduced energy consumption of the app. 13% (depending on the process).
- Smart sensors in the stenter allow monitoring of the complete machine bay a digital twin. Maintenance can be further optimized and productivity improved.
TexCoat coating unit
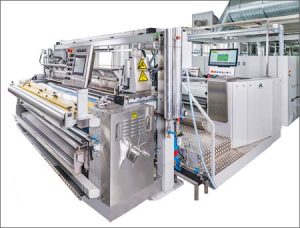
Monforts Texcoat coating machine is for multi-functional coating purpose, which integrates knife coating, magnetic roller coating and rotary screen printing. The multi-functional coating could be adapted to a wide range of applications for different fabrics and finishing demands. The control panel allows ease of mastering the control of all operation for the machines. The machine would be equipped with optional coating roller for knife over roller (CFK) which processes for highest accuracy. It is equipped with a fully integrated PLC control.
Monforts Smart Order
Monforts would show New Internet platform (Webshop) for easily identifying and ordering wear & spare parts with user-friendly visualization (specific to the respective machine).
Smart Support App
Monforts would release New Monforts app for direct communication of the customer to the Monforts service organization with new, advanced tools and functions to be used with smartphones (Chat, Video, White Board, Laser Pointer functionality, Teleconference).
XORELLA
Established in Switzerland in 1967 XORELLA has stood at the forefront in yarn conditioning and heat-setting ever since. Superior technology, reliability and precision were the foundation for the success throughout more than 5 decades. About 1.700 machines were sold to customers all over the world up to now. Since 2002 XORELLA is a member of the CHTC Fong’s Group.
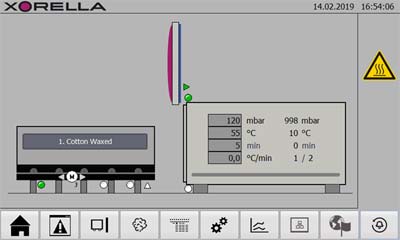
With the XO SMART and complemented by XO TREND since ITMA 2015 in Milano. XO SELECT series launched at ITMA 2007 in Munich demands of our worldwide customers can be satisfied from small capacity and manual handling to fully automatic vessels integrated in transport automation and packing systems from various suppliers. All machines feature the energy saving XO-heating system and can optionally be equipped with the waterless vacuum system XO Ecopac for maximized savings of precious resources.
XORELLA has listened to customers’ input and reengineered the controller and its software. At ITMA 2019, XORELLA released the latest generation hardware and software as well as visualization have been redesigned with a clear concept in mind: Easy operation even by less experienced staff in the mills.
There is a clear structure on all screens and the use of text was minimized. At the right side actual hazards are displayed with pictograms (such as high temperature in the picture below).
Textile Excellence
Next News
30 years of streat moisture solutions