DenimFWD’s “Urban Factory” Brings Textile Production Back To The USA
- Digital, sustainable and on-demand; changing the operating model, bringing back 15-25% of manufacturing production and initiating the necessary process of reindustrialisation.
- Digitally produced without polluting or increasing costs, producing what sells instead of selling what is produced.
- The first Handman in the USA, a new technology that revolutionises the jean industry with its automation.
The world’s first “Urban Factory” is opened by
Denim Forward, Inc (DenimFWD). A company for implementing advanced manufacturing and transformational technology,
DenimFWD is contributing to the return of textile production to the United States.
Located in the City of Industry, California (30 minutes from Los Angeles) the plant integrates revolutionary technologies that transform the textile industry production model into one that is on-demand, close to the customer and completely sustainable, digital, and automated.
DenimFWD is changing the operating model and bringing back 15-25% of manufacturing production to the US, initiating the reindustrialisation process needed in the textile industry.
Carlos Arias, CEO at
DenimFWD highlighted that the pandemic has accelerated local production and the change in the operating model: “which is why it is the moment to bring manufacturing back to the US boosting a new generation of industrialists and technological artisans, connecting creativity and production at the same time as changing how things are produced.”
He adds, “We are committed to revolutionary technologies that allow a 100% sustainable on-demand production close to the consumer, digitalising the whole process and improving the processes and product while also saving costs and speeding up time-to-market.” “With this
Urban Factory the consumer will decide to buy a product and that product will be finished in that moment and delivered that same day, eliminating stock.” This is a huge advance in the textile industry where 20% of garments produced are never used and end up in landfills or incinerated.
[caption id="attachment_23258" align="alignleft" width="300"]
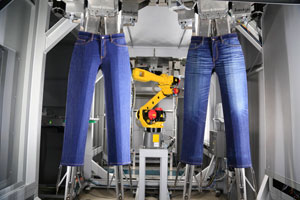
The first active Handman in the US[/caption]
Urban Factory: A complete transformation of the production model
Urban Factory is creating a complete transformation of the operating model in the denim industry. To do so
DenimFWD has teamed up with
Jeanologia (world leaders in sustainable and efficient technology development) as their expert technology partners.
Said Enrique Silla, CEO at
Jeanologia, “We are convinced that a new production model is possible, that’s why we have joined forces with companies from our industry such as
DenimFWD that share our values and objectives like Mission Zero, to eliminate 100% of discharge and pollution from jeans in all the world.”
He underlines that “
Urban Factory is the culmination of work carried out during the last few years and our contribution to the jeans industry to turn it into a case study that can be translated to the rest of garments manufacturing, starting a new era with a completely sustainable and digital production.”
[caption id="attachment_23259" align="alignright" width="300"]
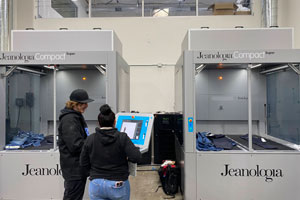
Jeanologia laser is an important technology being used in the “Urban Factory”[/caption]
On-demand production, sustainable and digital
DenimFWD’s
Urban Factory minimises delivery times and can produce up to 5,000 jeans and 4,000 t-shirts a day sustainably and efficiently. Its eco-sustainable operating model for advanced digital production integrates
Jeanologia hardware and software. These bring five fundamental benefits to the textile industry: being eco-efficient, scalable, agile, digital and having a neutral cost: connecting designers, producers, and consumers.
DenimFWD is transforming the industry by producing what is sold instead of selling what is produced, reducing operational costs and environmental impact, guaranteeing zero discharge.
Among the main
Jeanologia technologies used by
Urban Factory are laser, G2 Ozone, e-Flow, SmartBox, ColorBox, EIM (software for measuring environmental impact) and H2Zero (the first water treatment and recycling system that produces zero discharge without extra costs).
It will have the first active Handman in the US, allowing production automation with robots and humans to achieve agile, clean, and scalable production. Also, eDesigner will give designers a tool for making digital designing easier, faster, and more dynamic since what they see on the screen is what they get in the finishing.
Textile Excellence
Next News
asahi kasei celebrates 90th anniversary of bemberg™ business