LMW’s New Launches, Upgrades For Better Productivity, Quality, Sustainability
Lakshmi Machine Works Ltd., the platinum sponsor of India ITME 2022, has launched some interesting technologies and machines for the textile industry.
The Company has launched two new machines – Airjet LJS9 and Autowinder LAW 60. And a new After Market concept – LMW PACE – this is the latest aftermarket care suite from LMW for an exhilarating customer experience.
Also on display are:
- RAP – This is an upgrade of the existing Ringframe Auto Piecing system.
- Card LC 636 – An upgraded version - Carding machine with latest CDS and FIXFIL can changer
- Auto Leveller Draw Frame LDF3 2S
- Spinconnect – IoT Suite
Lakshmi Jet Spinning - LJS9
Salient features
- Self-reliant system for piecing to enhance efficiency and productivity
- Independent Drive system with seamless integration for easy maintenance
- Precise yarn traverse system for enhanced package quality
- Seed yarn piecing system for enhanced yarn joining quality
- Flexibility for different counts and materials within machine
- Double-sided machine helps for 40% space-saving
- Simultaneous piecing operation up to 24 drums to improve efficiency
Lakshmi Auto Winder LAW 60
Salient features
- Fully automatic winder linked to the Ring spinning frame
- Up to 60 winding heads per machine with winding speeds of up to 2000mpm
- Flexibility in material processing - Cotton, MMF & Blends
- Counts processed - 16’s to 100’s Ne
- Inverter controlled suction system to suit various yarn counts
- Doffer with fuzzy logic for efficient package removal and winding head restart
- Highly efficient bobbin preparation station with 30 bobbins/minute
- Up to 3 preparation stations to fulfil longer ring frames and coarser yarn counts
- Separate parking tracks for unprepared bobbins and rejected bobbins from the winding heads
- Spinconnect Ready
Ringframe Auto Piecing (RAP)
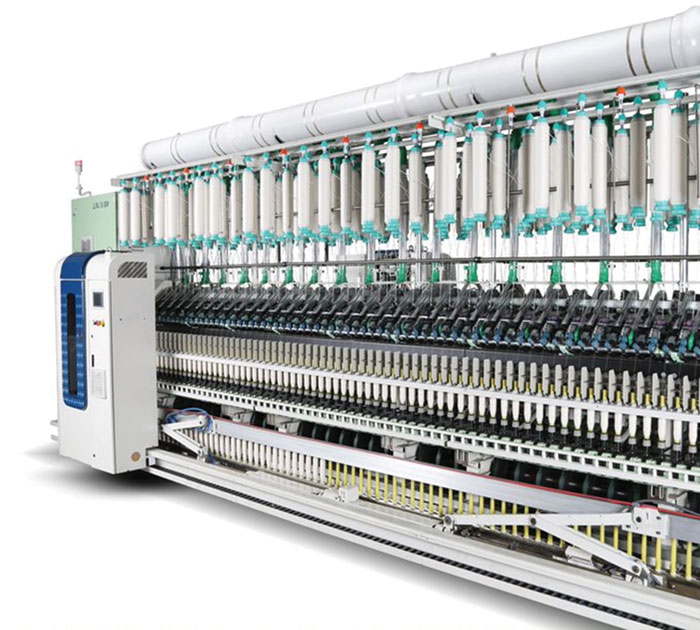
Ringframe Auto Piecing (RAP) is a fully automated yarn piecing system for ring spinning machine. The RAP receives information when there is a yarn break through YBS (Yarn Break Sensor) and travels to the particular spindle and automatically pieces the yarn instantly.
Salient features
- Higher Productivity due to automation of piecing
- Consistent and Enhanced yarn quality
- Lower dependency on manpower requirements
- Shorter piecing cycle time around 35s
- Patent protected technology
Manpower Savings
The biggest challenge faced by the spinning industry is shortage of skilled manpower, especially in Ring spinning. The piecer needs to be trained and skilled to do the piecing with lesser end mending time toavoid production losses. The Ring frame Auto Piecing (RAP) ensures auto piecing thus reducing the dependency on manpower.
Increased Productivity
Ring frame Auto Piecing (RAP) consistently works 24 x 7 around the year. The RAP unit receives signal from the YBS (Yarn breakage sensor) and travels directly to the respective spinning position and automatically mends the yarn. RAP captures the broken end from the package in the unique way without lifting the package, then inserts the yarn into the traveler and gets over pieced. The immediate attention to the broken end and auto piecing ensures higher productivity.
Precise Quality</strongRing frame Auto Piecing (RAP) ensures the consistent piecing length in the mended yarn. Auto Piecer also eliminates the contamination on the cop outer surface (through manual handling) which enhances and retain the quality of the yarn.
Flexibility
The unique design of Ring frame Auto Piecing (RAP) is suitable for both type of spinning technology, Normal Ring Spinning and Compact Spinning. It works ease on all applications.
Auto Leveller Draw Frame LDF3 2S
Salient features
- Twin Delivery Auto Leveler machine with independent drive arrangement
- Delivery speed of up to 1100 mpm (mechanical)
- State-of-the-art Auto leveling with Duo Digital concept
- 4 Over 3 Spring loaded drafting system with pressure bar
- Centralized roller setting with single tool and Centralized lubrication
- Coiler with Special finish bottom for best Coiling for Polyester rich process
- Display controlled Machine speed, Total draft, Coiler speed, Suction motor speed and Can speed (Optional)
- Kinetic back up Technology to manage power fluctuations and voltage variations.
- Linear Can Changer with 2 Reserve cans - Delivery Can size of 16” to 24” dia. and 42”to 48” can height
- Lower power consumption
- Less footprint
- Independent drive arrangement
- Ease of maintenance
- Easy and Independent motor drives
CARD LC636 S
CDS and FIXFIL Can Changer
Salient features
- Higher production up to 250 kg/hr
- Working width of 1500 mm
- Direct feeding to card with pressure regulated chute
- Swingable delivery duct for easy access (Patented)
- Smart Feed weight control system
- Multiple feed plate arrangement for highest degree of levelling
- Smart thickness measurement along with Metal detector and earthing stop motion
- Single Licker-in arrangement with pair of arcual combing segment
- External knife adjustment for easy waste management in Licker-in zone
- Separate Inverter drive for Cylinder and Licker-in
- Highest Active Carding Area of 1.95 m2 and Cylinder Area of 3.95 m2
- Aluminium alloy flats, 101 nos. with increased number of revolving flats (36 nos.)
- Brass clip with Improved flat (Patent applied)
- Replaceable end connector for flats (Patented)
- Optimum cylinder diameter of 1017 mm leading to lower thermal expansion and higher centrifugal force
- Automatic piecing aid
- Optimum waste extraction at right place
- Linear 40” x 48” coiler with high speed can changer
- Online quality monitoring system
OPTIONS
- Card with Drafting System (CDS)
- Fix-fil Can Changer for bigger can
CARD WITH DRAFTING SYSTEM (CDS)
Salient features
- Maximum speed up to 700 m/min
- 2/2 drafting system with servo control
- Pneumatic loading of top rollers – easy adjustment
- Auto levelling of sliver through Servo drive control
- Simplified yarn preparation process for Airjet, Ring Spinning & Open End
FIX FIL CAN CHANGER
Salient features
- Can changer mechanism with minimal movement of can, inside the machine (Patent applied)
- Improved efficiency - No reduction in running speed during can changing
- Dual can plate with individual drive arrangement - Less Mechanical & No Pneumatic Components
- In built can pusher arrangement - Operator Friendly
- Doffed can monitoring sensor - Safety and Intelligence in-built
- Can dia. up to 1200mm with height of 1200mm - Increase in can content up to 50%
- Improved Card and Draw frame efficiency due to minimal can movement, reduced number of doff and reduction of piecing in Draw frame creel
SpinConnect
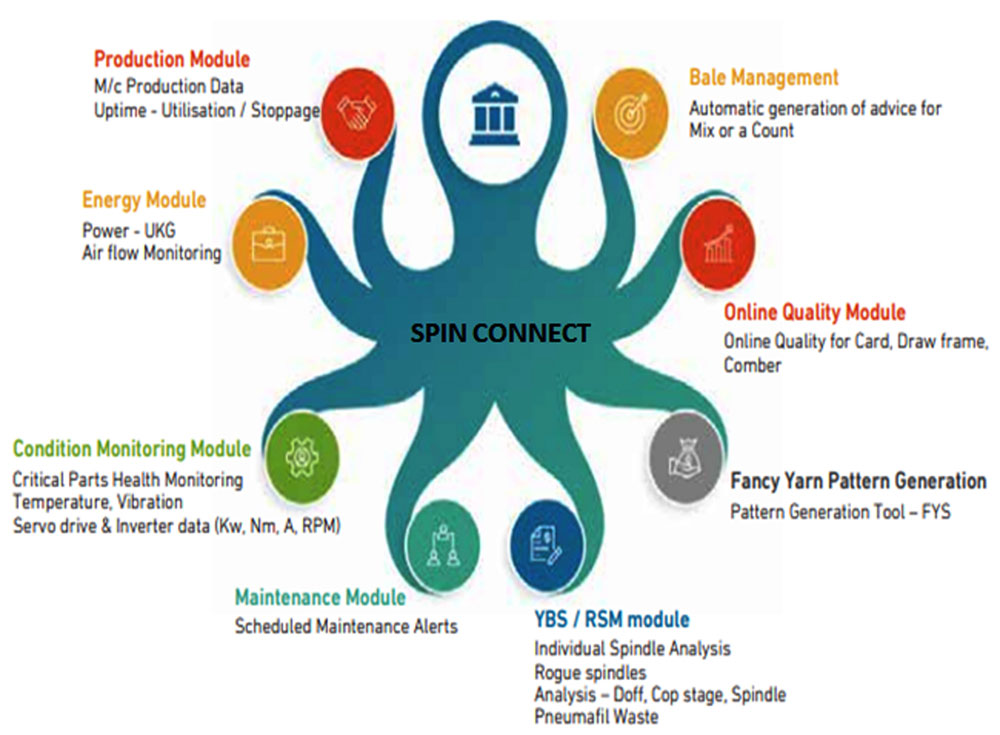
LMW’s Spin Connect, a web-based monitoring and control system is an all-in-one application that provides the overall view of spinning mill’s performance in a single window. The digital system connects all machinery and provides information on production, quality, maintenance, etc. so that management team, technical team, operators can monitor, and manage / maintain spinning mills. This system enables to optimise processes and effectively utilize resources resulting in cost saving and increased profits.
Textile Excellence
Previous News
the dull textile economic situation and what the industry can do
Next News
ntc to become world class textile company: textile minister